Rain Carbon Inc. is one of the world’s largest producers of calcined petroleum coke and coal tar pitch -- essential raw materials for a range of industrial processes and products.
With an annual capacity of 2.4 million metric tons of calcined petroleum coke (CPC), Rain Carbon Inc. is one of the world’s largest producers of CPC, which is a crucial ingredient in the anodes used during the electrolytic production of aluminum worldwide. We're also a global leader in the production of coal tar pitch, which acts as a binder in the carbon anodes used for aluminum production.
- Cathodic protection and electrical grounding for underground construction
- Packing material for anodes during the baking process
- Carbon raisers used by the steel industry
- Electrodes for steel recycling
Many of these applications are directly related to recycling of sustaining product life, and require energy to produce. The high temperature generated within the calcining process provides a significant opportunity for energy recycling and conservation.
- Calcination Products
- Coal Tar and Petroleum Distillation Products
- Energy
- Carbon Black Oils
- Impregnation Oils
- Other Oils
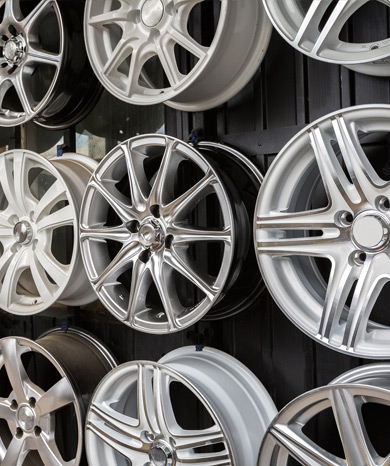
Calcined petroleum coke (CPC) is created from green petroleum coke (GPC), a by-product of refining crude oil. While CPC can be created using a number of processes -- including rotary kiln, hearth and vertical shaft technologies -- the high-temperature conversion from green coke to calcined coke alters the material in key three ways:
- Drying
- Release of residual hydrocarbons
- Densification
This is accomplished as the coke is heated from ambient temperature to a finishing temperature of about 1,350°C. Although initial start-up of the process uses an external fuel such as natural gas or fuel oil, the vast majority of heat required to sustain the process after start-up comes from the in-situ combustion of the residual hydrocarbons inherent in the coke, and only oxygen is needed to maintain that combustion.
CPC is an essential ingredient in the production of aluminum. In fact, every ton of aluminum needs approximately 0.4 tons of CPC, making Rain Carbon a critical "carbon link" between the refineries and the aluminum industry. CPC also is in great demand for the production of titanium dioxide (TiO2).
Today, Rain Carbon is one of the world’s largest producers of calcined petroleum coke, with seven plants in the United States and India producing a combined 2.4 million tons per year.
Phone: +1-985-635-3400
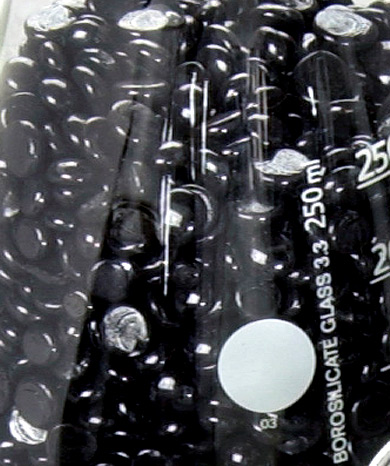
Pitch Products
Pitch products are produced by Rain Carbon Inc. from coal tar pitch (CTP), a derivative of coal tar distillation, as well as from specialty petroleum feedstocks. CTP is mainly used as a binder for the production of carbon anodes essential for aluminum smelting. An important variation of CTP also serves for impregnation of graphite electrodes employed by electric arc furnaces in steel production. Rain Carbon offers its customers a broad range of coal tar and petroleum pitches with different properties for the widest spectrum of applications.
Pitch Products
- Coal Tar Pitch
Rain Carbon manufactures CTPs with many different softening points, used as binders for carbon anodes, graphite electrodes, specialty graphite, and Søderberg electrodes, as well as for refractory materials. - Impregnation Pitch
Rain Carbon produces pitches with properties suited to the impregnation of graphite electrodes, carbon cathodes, specialty graphite, and refractory materials. - Specialty Tars
Rain Carbon creates special tars with different viscosities for the production of monolithic refractory products. - Refined Tars
Rain Carbon produces its RT-12 tar for use in sealing road surfaces in North America. - Petroleum Pitch
Rain Carbon also creates petroleum-based pitches for road surface sealing, and for the production of clay pigeons and activated carbon. - Pitch with high softening temperature
Rain Carbon engineers pitches with softening temperatures between 150 and 200°C (300 and 390°F), which is essential to the manufacture of specialty graphite.
Phone: +49 2305 705-157
Fax: +49 2305 705-446
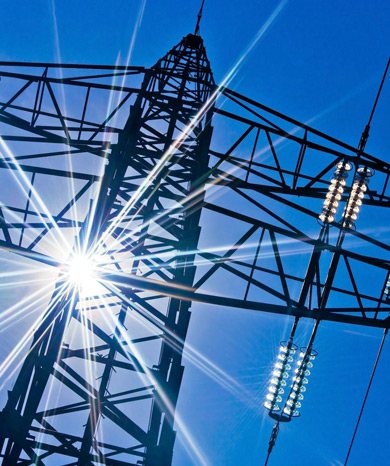
Resourceful waste-heat recovery saves energy and protects the environment. The high temperature generated within the calcining process provides a significant opportunity for energy conservation and recycling. Process-heat recovery reduces greenhouse gas emissions and critical air pollutants, and results in a more carbon-neutral co-generation of energy. As part of Rain Carbon’s commitment to a clean and efficient industry that works in harmony with the environment, the company has made a significant investment in heat-recovery systems at five of its calcined petroleum coke (CPC) facilities, with a generation capacity of approximately 125 megawatts.
These heat-recovery projects co-generate electric power from waste heat recovered in the calcining process. Energy recycling is accomplished by first causing the complete combustion of residual hydrocarbons and any solid carbon emerging as an exhaust from the calcination process, and then capturing this thermal energy in a heat-recovery steam generator. The resulting high-pressure steam is used to generate electricity or to provide thermal heating for other industrial processes. This conserves the use of additional fossil fuels. The combination of energy recycling with calcining therefore achieves the simultaneous benefits of CPC production and energy conservation.
Most of the electricity recovered from the calciners is sent to the regional power grids for transmission to local users. Rain Carbon has entered into agreements with local utilities for the supply of power. Based on the national averages for electric power production, the co-generation plants will reduce greenhouse gas emissions by more than 150,000 tons per year. This reduction occurs because the project generates power without burning additional fossil fuel and by recycling heat energy from the calciner exhaust.
Rain Carbon also co-generates energy at four of its distillation and advanced materials facilities, with a waste-heat recovery steam generation capacity of approximately 59 megawatts. The resulting energy is used to power internal process or is exported to electric power grids and industrial partners.
Phone: +49 2305 705-157
Fax: +49 2305 705-446
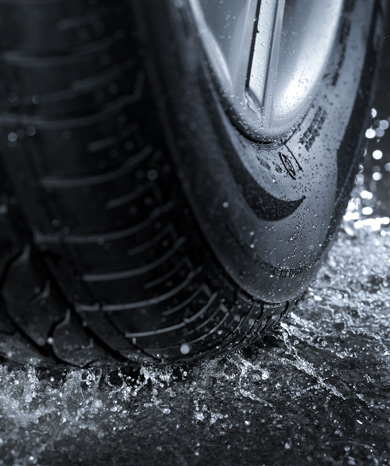
Tar oils are used in the production of carbon black feedstock. Rain Carbon produces specially designed, high-tech carbon black oils that are used as feedstocks that are converted by our customers into industrial carbon black for a wide variety of uses, including pigments for plastics, rubber and printer toners. The most important application of carbon black is in the tire industry, where it improves a range of performance properties including sidewall strength, rolling resistance and traction. Carbon black also increases tire life by improving wear resistance and UV protection.
Phone: +49 2305 705-459
Fax: +49 2305 705-446
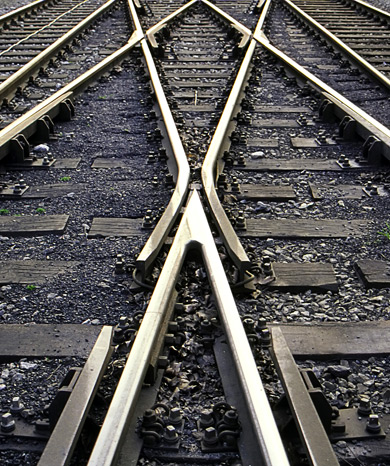
Creosote oils or impregnation oils are used to preserve wood products, such as railway tie sleepers, and utility and telephone poles. Impregnation oils were the core products around which the RÜTGERS Group was originally founded in the 1800s. Today, as Rain Carbon, the company still produces creosote oil, mainly for use in the North American impregnation market.
Phone: +49 2305 705-459
Fax: +49 2305 705-446

Rain Carbon Inc. offers a wide range of oils including heating oils for industry, fluxing oils for road building, oil and gas exploration, bunker oils and wash oils.
Phone: +49 2305 705-459
Fax: +49 2305 705-446