Sustaining Ecosystems
Society depends on nature and the environment for essential, life-sustaining needs such as clean air, water and food. We aim to maximize positive and minimize the negative impacts on the environment arising from our operations.
Waste Management
We recover hazardous and non-hazardous waste as much as possible. Since many of our primary products are made from by-products from the petroleum and steel industries, we effectively and efficiently reduce product waste from those and other industries while also maximizing the carbon productivity of their by-products. It is our ambition to foster the exchange between sites to realize synergy potentials.
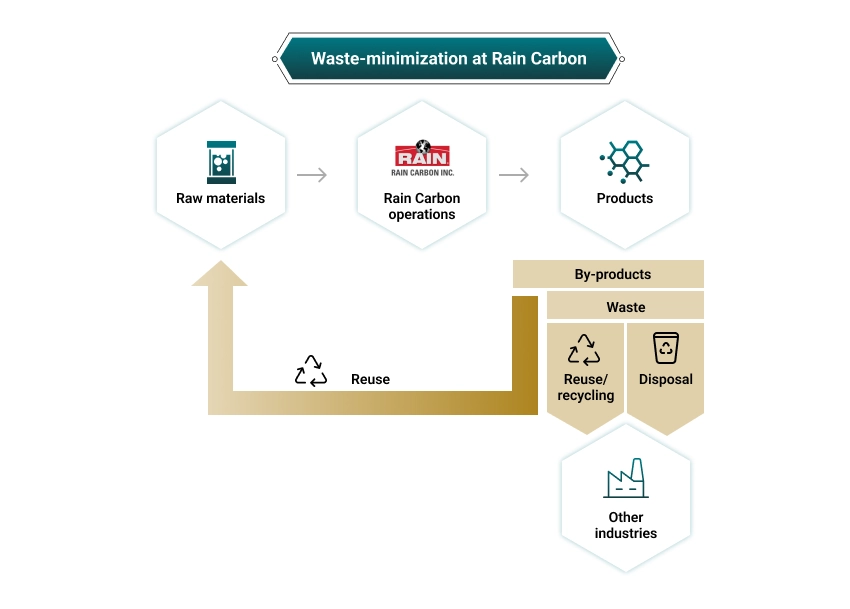
We have state-of-the-art flue-gas desulfurization (FGD) systems and leak-detection and -repair (LDAR) programs to ensure we monitor our air emissions closely. We aim to reach the highest level of resource efficiency in converting as much raw material as possible into products, thereby minimizing waste and wastewater volumes.
State-of-the-art FGD systems
Rain Carbon has lime-based flue-gas desulfurization (FGD) systems installed at our calciners at:
- Vizag, India since its commissioning in 1998
- Lake Charles, U.S. in 2013
- Chalmette, U.S. in 2015
- Norco, U.S. in 2017
FGD systems reduce SO2 emissions by up to approximately 98% at Vizag, 65% at Chalmette, 60% at Lake Charles and 40% at Norco. We will continue to craft and implement innovative, cost-effective solutions to reduce our environmental impact, thereby fulfilling our responsibility toward the planet.
At our new vertical-shaft calciner in the Andhra Pradesh Special Economic Zone in India, we have installed a state-of-the-art liquid-ammonia gas-scrubbing technology. This advanced FGD system will enable us to virtually eliminate the plant’s SO2 emissions. An added benefit is the production of a valuable by-product, ammonium sulphate, which will be provided as a fertilizer to farmers in India, making it a highly sustainable process.
In July 2021, Rain Carbon engaged The Council of Scientific Industrial Research – National Environmental Engineering Research Institute (CSIR-NEERI) to perform an independent assessment of the positive impact of our pollution-control activities, as part of the company’s effort to gain unre¬stricted access to GPC and CPC imports. In September, CSIR-NEERI published its report, which looks specifically at the reduced emissions resulting from the use of FGD and waste-heat recovery systems for electricity generation at our Visakhapatnam calcination facility and the new vertical-shaft calciner in the Andhra Pradesh Special Economic Zone.
In terms of our two Indian plants’ state-of-the-art FGD systems, CSIR-NEERI concluded that they have more than 98% scrubbing efficiency, thereby making them among the cleanest CPC manufacturing units from an environmental perspective.
Leak-detection and repair program
We have implemented a leak-detection and repair (LDAR) program at our carbon distillation and advanced materials plants to proactively and regularly check for fugitive losses of hazardous benzene, toluene and xylene (BTX) emissions. The program was initiated in 2010 at our Zelzate facility in Belgium, and due to its success, a similar program was rolled out at our Castrop-Rauxel, Germany and Hamilton, Canada carbon distillation facilities. Each year, an external company performs a comprehensive audit to identify BTX leaks. Detected leaks are then repaired as soon as possible. The LDAR project enables us to constantly monitor and reduce hazardous BTX emissions at our facilities and is a major contributor to continuously minimizing our environmental impact.